Project Description
The in-line dyeing plant for the production of denim fabric consists of 1 production line and 1 color kitchen plant in Vietnam.
The line is about 100 meters long and has a height of about 6 meters and a maximum working speed of 35 m/min.
The kitchen is about 20 meters long and about 7 meters high.
The line is about 100 meters long and has a height of about 6 meters and a maximum working speed of 35 m/min.
The kitchen is about 20 meters long and about 7 meters high.
The system was installed and put into production between October 2016 and February 2017; the installation and start-up were performed correctly and with excellent results.
After about 18 months, due to a structural problem of the flooring of the machine positioning site, the machine collapsed laterally.
The customer requested a prompt intervention for the restarting of the machine (in a short time).
After about 18 months, due to a structural problem of the flooring of the machine positioning site, the machine collapsed laterally.
The customer requested a prompt intervention for the restarting of the machine (in a short time).
The operations started in August 2018 and ended in October 2018 (the intervention was suspended for about a month to allow the customer to reconsolidate the floor).
Sequence of operations:
- Verification of the conditions of the work site.
- Checking the condition of the machine structure.
- Pneumatic line removal.
- Steam and water line removal.
- Disassembling color circulation system.
- Dismantling of the structure.
- Dismantling of dyeing and washing tanks.
- Reconsolidation of the floor.
- Repositioning of the tanks.
- Alignment and leveling of the tanks.
- Replacement of machine structure.
- Alignment and leveling of the structure.
- Replacement color circulation system.
- Conduit positioning.
- Machine rewiring.
- Reinstallation of the pneumatic line.
- Reinstallation of steam and water line.
- Mechanical start.
- Putting into production.
In order to carry out the intervention in the shortest possible time, the strategy used to solve the critical issues was to disassemble the machine in a modular way.
The solution was to disassemble the structure, the pipes and all the modular units, trying to dismantle as few parts as possible, speeding up the disassembly and subsequent reassembly operations. This allowed us to satisfy the customer’s requests and to respect the agreed timescales.
The solution was to disassemble the structure, the pipes and all the modular units, trying to dismantle as few parts as possible, speeding up the disassembly and subsequent reassembly operations. This allowed us to satisfy the customer’s requests and to respect the agreed timescales.
The commissioning of the plant was carried out within the agreed time frame and to the customer’s satisfaction.
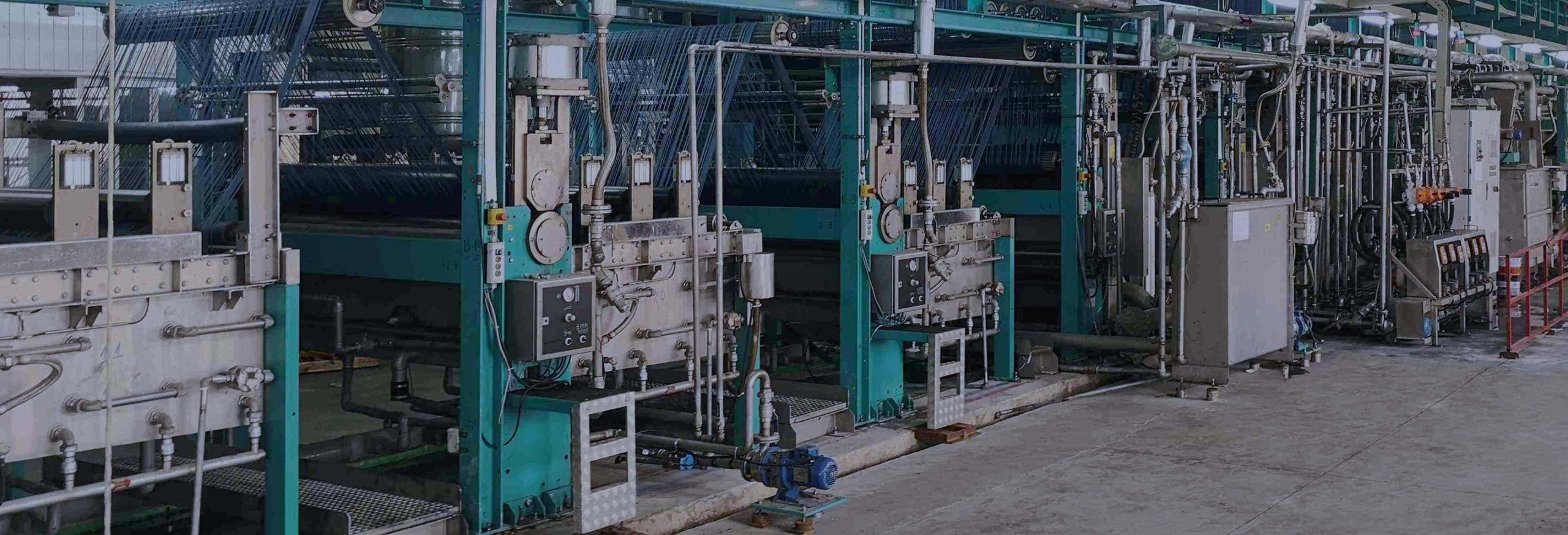