Project Description
The rope dyeing plant for the production of denim fabric is located in Algeria. It consists of 2 production lines, 1 color kitchen plant and 3 sizing machines.
The two lines are about 100 meters long each and were about 9 meters high with a maximum working speed of 50 m/min.
The kitchen is about 30 meters long and about 7 meters high.
The 3 sizing machines are new generation with vertical marl and their maximum working speed is 180 m/min.
In the work area there were several companies, with consequent technical and safety problems.
The operations were part of a much larger project. It was an important investment of about 2.5 billion dollars and was spread over an area of about 1,000,000 m2 that when fully operational would have given work to about 25,000 people.
Another critical factor was the delay in the start of the assembly operations, due to problems with the completion of the infrastructure works.
Consequences of these problems were the requests by those responsible for assembling the two lines at the same time, but given the conditions under which it was necessary to operate, it was completely impossible to satisfy them.
Sequence of operations:
- Preparation of the building site with control of the masonry works at the customer’s expense.
- Centre line tracing for machinery positioning.
- Positioning Dyeing Tubs.
- Preparation and positioning of support structures Return cylinders and dancers.
- Vaporization and Oxidation Positioning.
- Assembly Sizing machines.
- Montaggio Imbozzimatrici.
- Coiler Assembly.
- Kitchen assembly.
- Piping assembly.
- Plant wiring.
The solution developed was to assemble the lines in a differentiated way. Specifically, we started the assembly of one line and when the site conditions allowed it, we started the assembly of the second line.
This made it possible to satisfy the customer’s requests and to respect the agreed timescales.
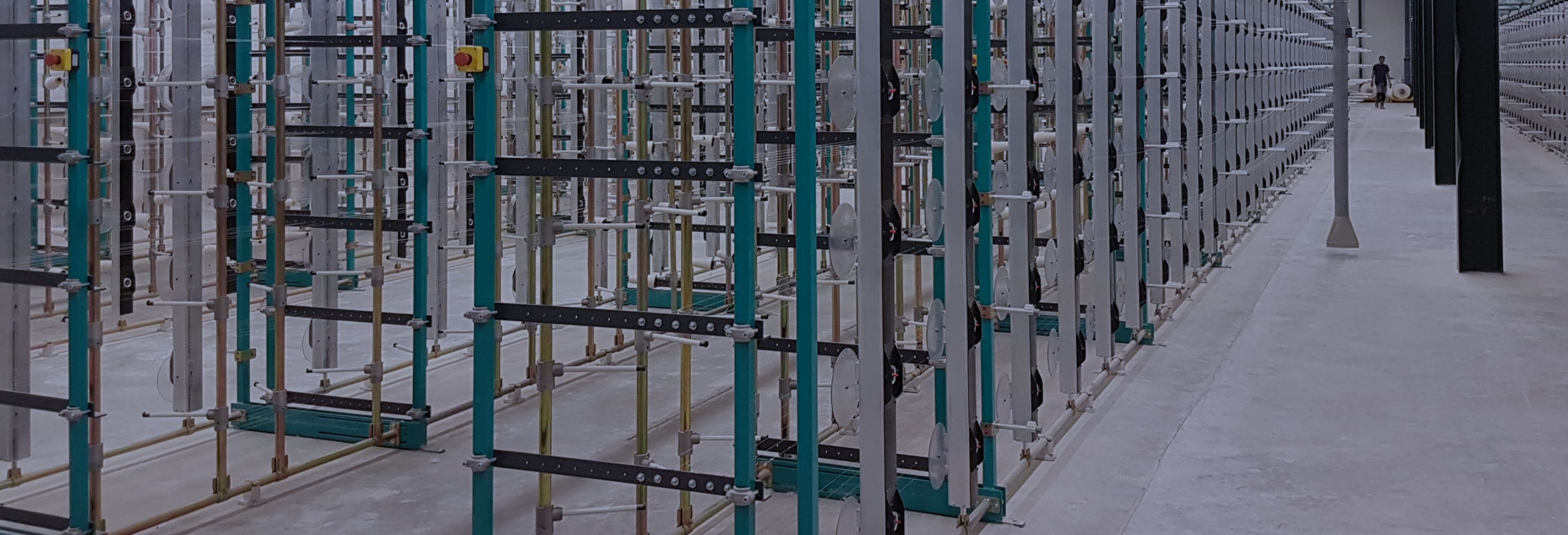